The third phase is steel section and accessory manufacturing. After receiving production drawings from the technical department, Bao Dung Steel factory will start the manufacturing process. All components of the project are manufactured at Bao Dung Long An – a modern steel structure factory with a capacity of 12,000 tons / year in Long An, Vietnam.
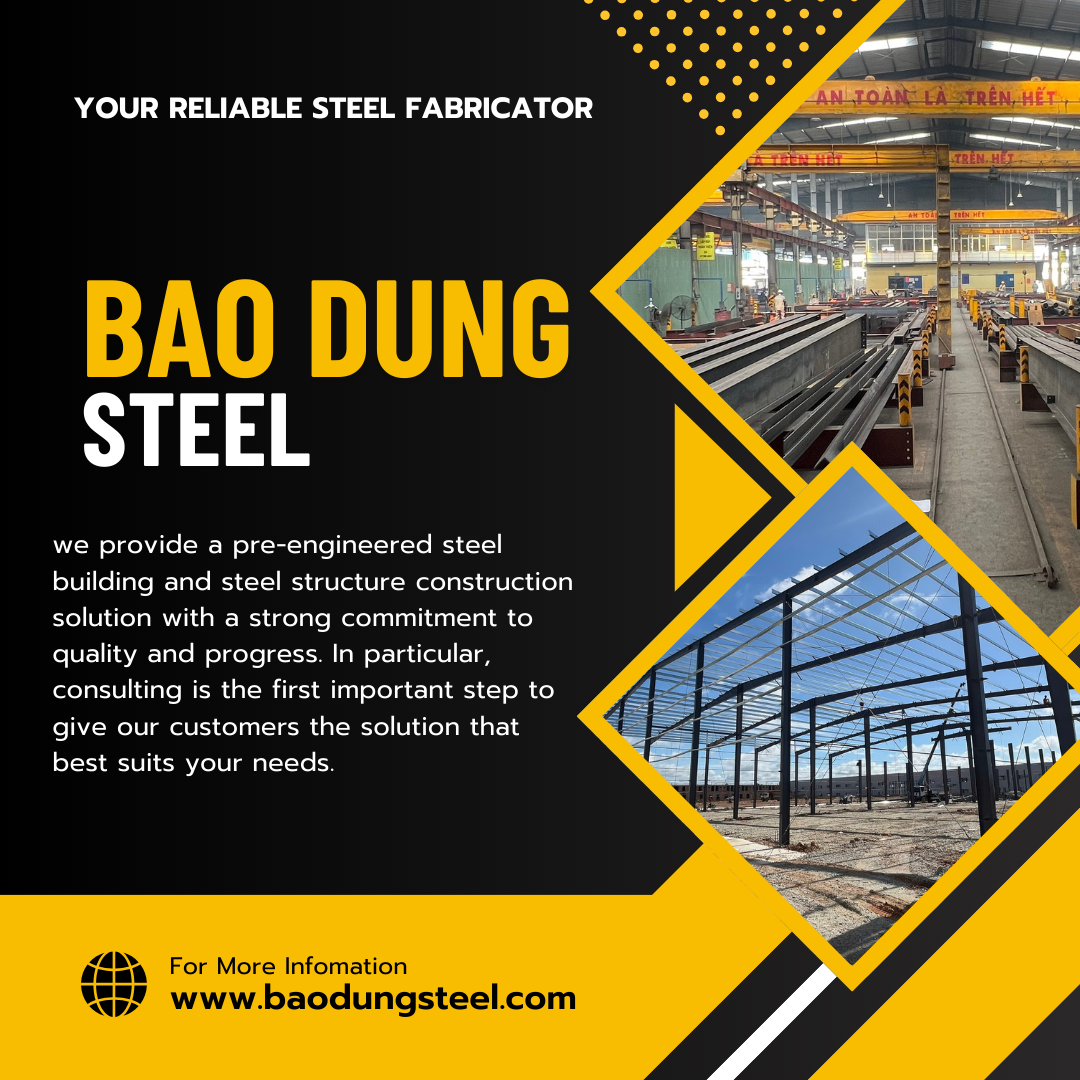
We focus on improving quality, productivity & process time through scientific and engineering practices. The advanced production line is arranged in a U-shaped structure, which is also the product production sequence. As a result, we optimize production speed, organize our workspace efficiently and safely for employees. At the same time, we apply the international quality management system ISO 9001: 2015 and the Occupational Safety and Health Management System Standard 18001: 2007 for all factory operation and production activities. Therefore, Bao Dung Steel Structure always ensures product quality and delivery schedule as committed.
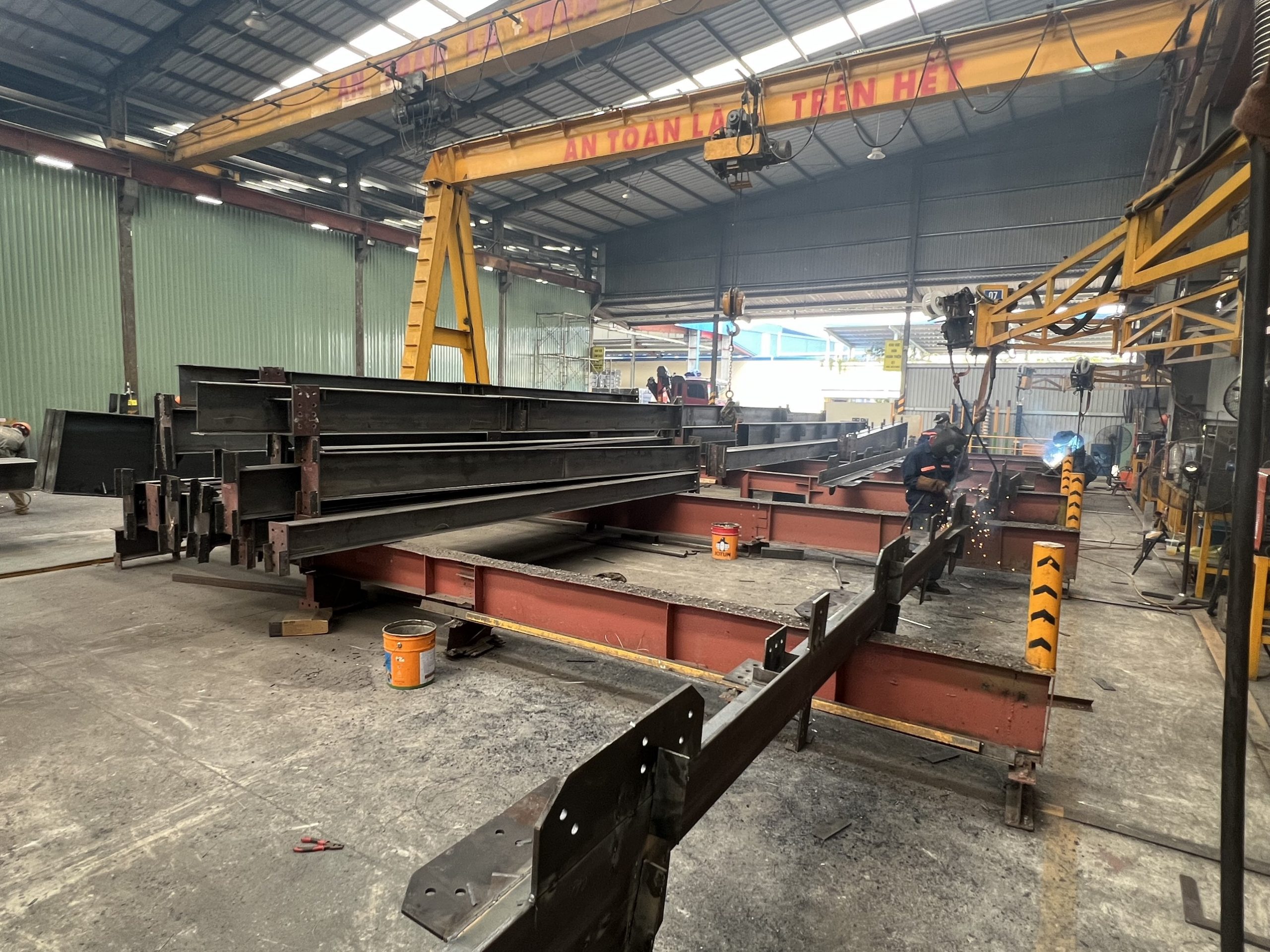
We will introduce the production processes of 3 main parts that build up a pre-engineered steel building including:
- Primary members: beams, columns …
- Secondary members: purlin, door…
- Sheeting: roofing sheet, cladding, wall …
- In addition, Vis factory also produces accessories such as downspout, valley gutter, eave gutter, canopy…
1. Primary members
Cutting
Steel sections have 2 basic types: hot rolled steel section and steel built-up section.
Hot rolled steel sections are made of hot-rolled steel which are rolled through the mill into the particular shape such as I beam, H beam. With this type, we need to cut off the excess part so that the rest is sized to match the design requirements.
Built-up steel sections are composed of other smaller members into beams with an I or H cross section. The input material of a built-up steel section is steel plates or coil. Then the plates are cut precisely to the exact shape and size in the production drawing. The steel plates will have different thickness depending on the design requirements.
At Bao Dung Steel Structure, with a strong investment in a system of highly automated equipment, we can own a variety of cutting technologies for production. We have a wide range of cutting machines suitable for various thicknesses of steel plates such as CNC automatic cutting machines, CNC plasma cutting machines, laser cutting machines, mechanical cutting machines…
rilling and punching:
After cutting, use the automatic or semi-automatic drilling machine to drill or punch holes on the cutter plates as required.
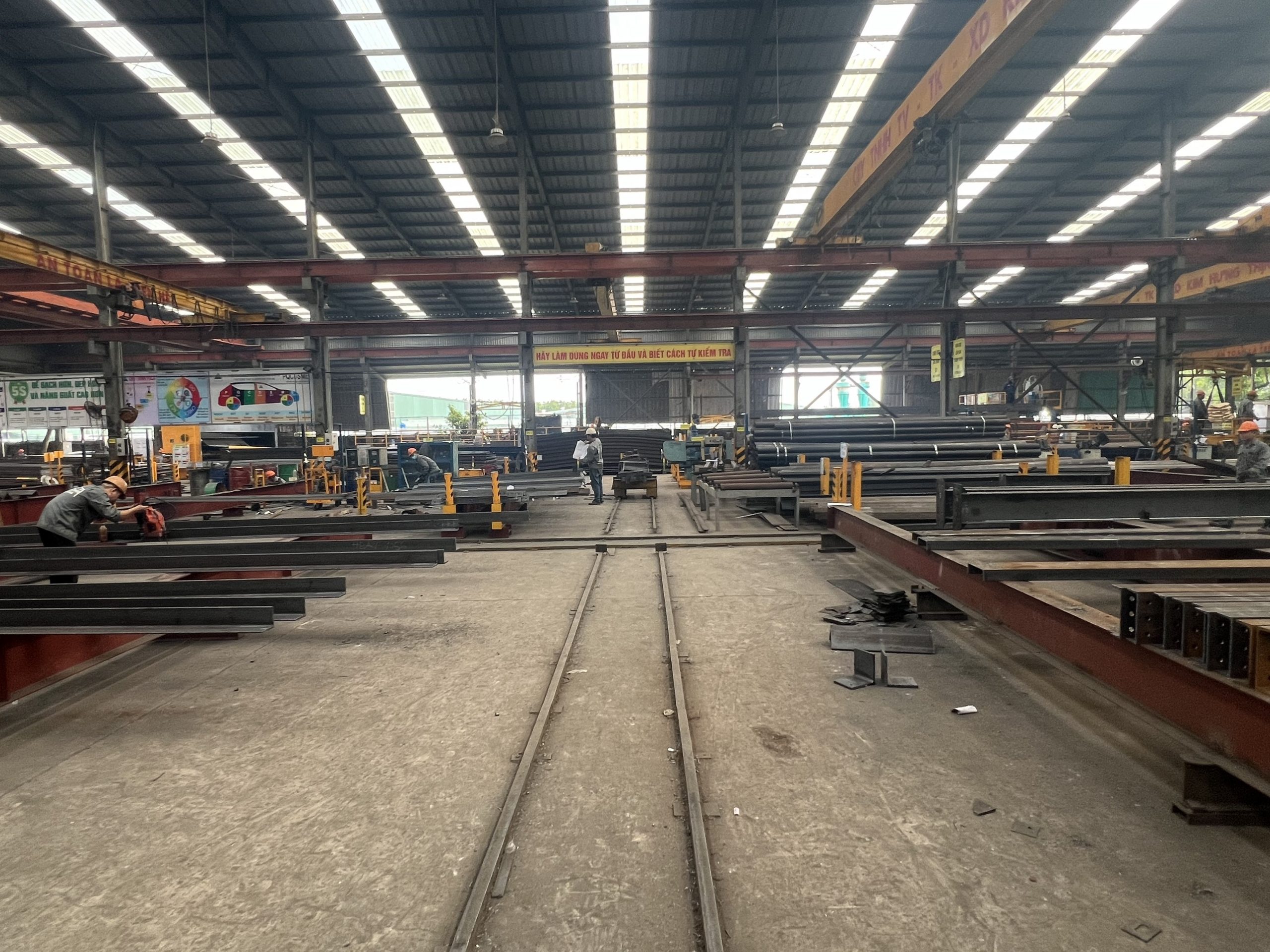
Assembling:
At this step, we use automatic or semi-automatic assembly machines to assemble the beam (or column) by connecting flange and web plates with temporary welds.
Welding and connection details welding
After assembling, components are transferred to the next procedure of welding two flanges of steel plates. We apply modern welding technology according to the welding procedure approved by AWS American Welding Association Standards. Therefore, we create good welds that are uniform in width; the ripples are even and well feathered into the base metal, which shows no burn due to overheating.

Straightening
The high temperature during welding can deform steel beams. If we don’t solve this problem,steel beams will not be possible to erect at the site. Therefore, the components must be straightened and checked again before moving to the next step.
Gusset plate welding
In this step, the gusset plate is hand-welded on the main beam web by highly skilled welding workers
Surface cleaning
Built-up steel sections are cleaned physically or cleaned by using shot blasting machines, depending on the customers’ choices.
2. Secondary members
Forming
The raw materials are galvanized, colored or cold-rolled black steel coils that meet ASTM international standards. ForZ or C purlin, they will be shaped from cold-rolled steel with a thickness of about 1.5 to 2.5 mm.
Cutting, punching or drilling
After being formed to the correct shape, these components are cut and punched according to details on the production drawing
Painting
Depending on the case, the purlin, after forming, will be painted or unpainted. If the purlin is made of hot rolled – black steel sheet, the purlin will be cleaned and painted to ensure the durability and aesthetics of components.
3. Sheeting
Sheeting (roofing, wall) is formed at Bao Dung factory, or some special panels (such as Vis Lokseam) are made at the site. The materials are hot-rolled, cold-rolled, galvanized and colored steel coils according to ASTM international technical standards
Painting
The coating has a great influence on the durability of steel sections during construction and during use time. Besides, the coating also determines the pre-engineered steel building’s aesthetics. Therefore, Bao Dung Steel Structure uses high pressure industrial spray guns with American technology that creates a tough, durable and beautiful finish. Normally, the steel section has 2 layers of coating: the first layer is anti-rust coating, the second one is protective coating. The thickness of this coating is about 80μm or more to ensure the long service life of sections.
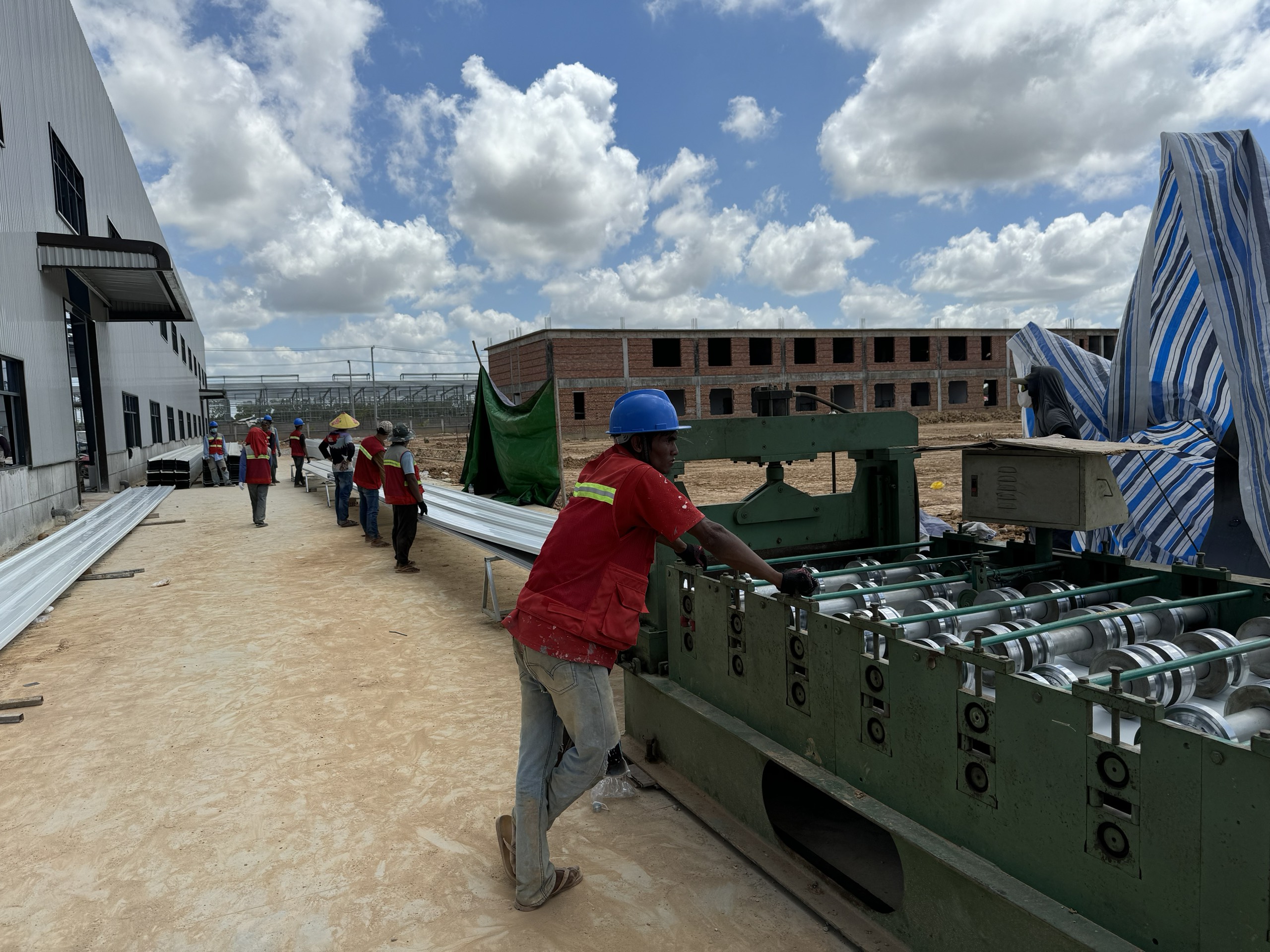